At present, the grinding roller forms used in vertical roller mills in various industries can be divided into two types according to the shape, namely, conical roller and wheel roller.
As a professional cement equipment parts manufacturer, Zhili New Materials can manufacture matching mill rollers for customers according to their drawings or VRM models. We have continuously developed and improved the production process and manufacturing technology over the decades of the production process. At present, we have mature VRM grinding roller production technology. We are committed to improving the wear resistance of the roller of the vertical mill, optimizing the grinding process, and helping customers save maintenance costs.
The materials of the grinding roller we produce are mainly high chromium cast iron, high chromium + surfacing, Medium alloy steel(alloy studs) + surfacing, ceramic alloy composite, etc.
High chromium + surfacing
The most material of grinding roller is high Chrome,add the surfacing welding can extend lifetime and reduce costs and improve efficiency.Surfacing welding include Welding wire hard facing and Alloy studs inlaid surfacing welding.
Welding wire surfacing grinding roller improves the wear resistance and service life by surfacing wear-resistant welding wire on the surface of the roller body.
Medium alloy steel(alloy studs) + surfacing
The Alloy studs inlaid surfacing welding vertical grinding roller is designed according to the working conditions and the wear resistance curve of the product. In the wear area, the powder metallurgy technology and surfacing technology are combined, and the special welding materials are used to form the inlay welding structure and metallurgical combination, improve the wear resistance and service life of the product, and achieve the regenerative repair to improve the service life of the product.
Ceramic alloy composite
The ceramic alloy composite grinding roller combines the characteristics of ceramic and alloy. It has both the wear resistance of ceramic and the mechanical properties of alloy, and is not easy to break or fall off. Due to the different properties of ceramic and alloy, the height difference of the surface is caused, thus forming a honeycomb structure, which increases the friction force and effective contact area of the surface, and helps to improve the grinding or crushing efficiency.
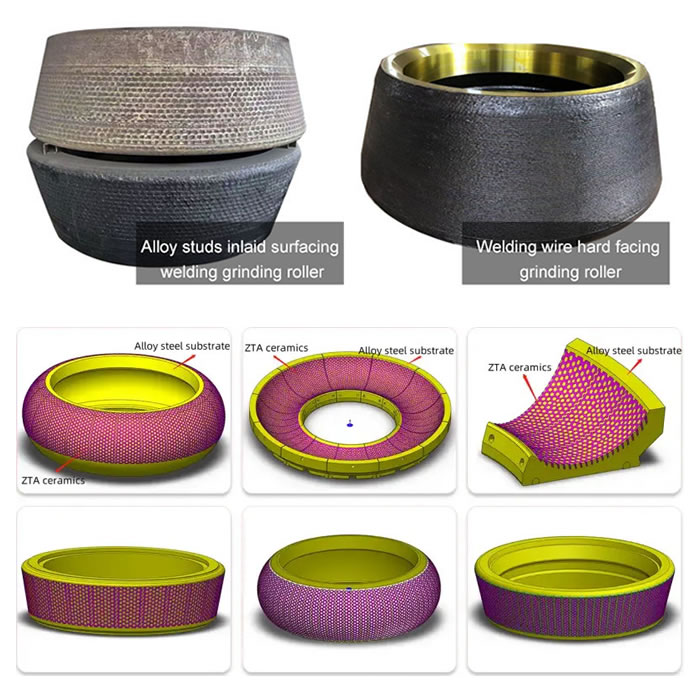
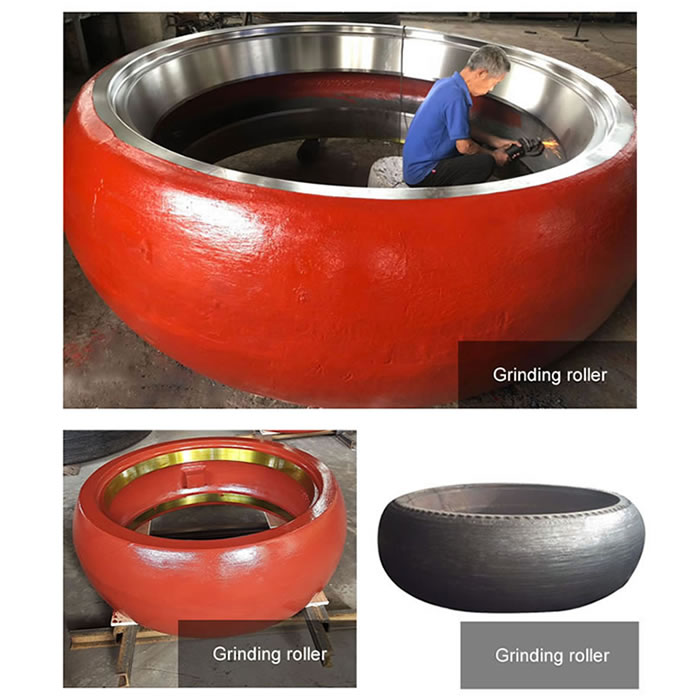